Author: Steve Henning
Originally in Trenchless Technology Magazine April 2019 Issue
As trenchless technology continues to become more universally accepted and new materials are being developed and proven successful, we are beginning to see more “outside of the box” applications, if you will.
For a full structural restoration, it wasn’t that long ago when the use of a trenchless technology typically meant one of three applications: CIPP, slip lining and pipe bursting. But over the last decade, with the advancement of new products and application methods, it now possible to obtain a fully structural repair using spray applied technologies. One such material capable of this is geopolymer mortar.
In the case of Lakewood, Ohio, it was the perfect solution to repairing an aging and badly deteriorated drop manhole and outfall culvert.

129-ft Deep Manhole and 350-ft Long Egg-Shape Outfall Challenges
In the Lakewood suburb of Cleveland, Ohio, a 129-ft deep brick manhole and 350-ft long culvert system, constructed between 1912 and 1915, had seen better days. Located along the West Branch Rocky River, at a T-section where Madison Avenue ends at Riverside Drive, it was time to repair these sewer sections. The passage of time and the ever-present flow of roadway salt had caused severe corrosion to the manhole baffles and the intrusion of groundwater. The owner was also concerned about the system’s overall structural integrity. However, there was no simple solution for repair.
The manhole’s original construction was impressive, not only in depth, but its diameter, as well. It expanded from 4 ft to 8 ft in diameter from top to bottom. Equally impressive was the 78-in. H x 66-in. W egg-shape brick culvert extending from the bottom of the manhole to the outfall. It, too, was suffering from degradation. The challenge for the culvert rehab was different than the manhole. In this case, it was the location. Access to the outfall was extremely difficult as it was located at the bottom of steep embankment along the river’s edge. Then once there, the culvert went 350 lf into the side of the embankment to reach the drop manhole base.
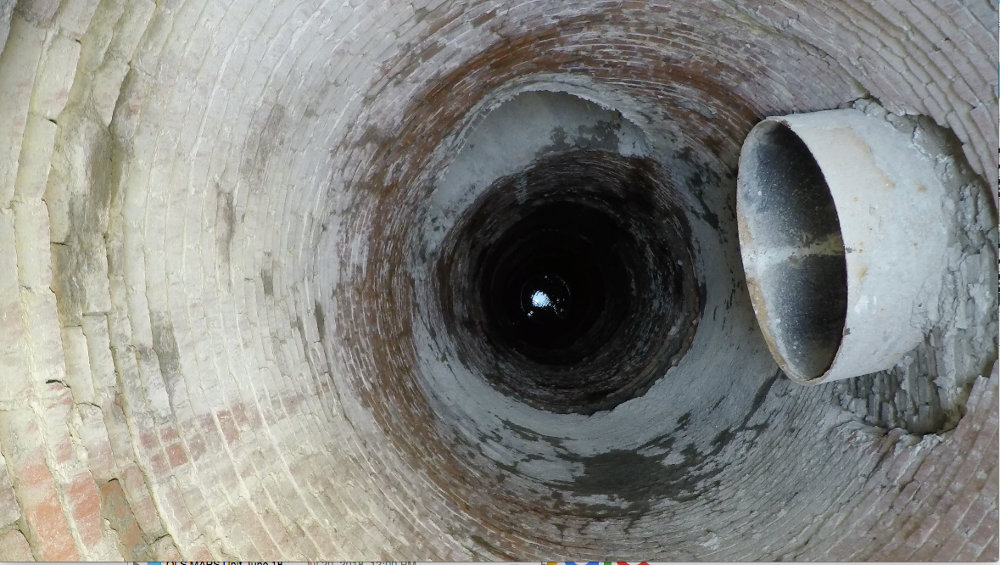
Solution: Two-Pronged Approach to Rehab
Because of the extraordinary depth of the manhole and odd shaped culvert, a spray-applied lining solution was recommended. To address the manhole, the design was broken out over ranges of depth with the installed material thickness increasing as the lining got deeper into the manhole. The design also took into account soil, traffic and hydraulic loading on the manhole, across its full depth. Similar consideration was given for the outfall culvert, which resulted in two installation thicknesses to complete the task. A thicker lining was applied at the base of the manhole where it was deepest, with a decrease in the liner thickness as it neared the outfall, where the depth was shallower.
Given the age and degraded condition of the manhole in addition to the shape of the culvert, a geopolymer lining system was chosen for its excellent performance, handling and application characteristics. Sewers are known to be harsh environments in which construction materials need to be carefully selected in order to perform. This project site was no exception. During periods of normal wet weather flows (less than 1-in.) the sewers are prone to low flows, allowing for the settlement of solids, only to be stirred up and become abrasive as larger rainfall events are introduced. Due to the extreme depth of this manhole, the effects of rain induced sediment rich flow is further compounded and can cause more damage to the structure over time.
Ultimately GeoKrete Geopolymer was selected as the spray applied lining material because of its ability to resist I&I, to form a new structurally independent manhole or pipe inside the existing structure(s) and its exceptional abrasion resistance.
The Application Process
By using a geopolymer mortar spray application process, several critical and challenging project concerns were addressed: extreme manhole depth, the gradual increase of I&I, and ability to start and stop the application with no adverse effects. Since the manhole was so deep, a special basket attached to a winch and crane was used to hold the spray application crew. The crew then had to be lowered into the manhole to spray apply and hand trowel (to a smooth finish) the geopolymer. When each section was completed, a crew member would radio the crane operator with instructions to lower the basket to the next stage. This step was repeated though the process.
RELATED: Quadex GeoKrete Geopolymer Passes Critical European Biogenic Acid Corrosion Test
Due to accessibility limitations, the entire length of egg-shape brick culvert was lined from a single access point, which was at the top of the manhole. The geopolymer’s ability to be pumped from equipment at street level, then down 129 vf through the manhole, and, ultimately, another 350 lf through the culvert is a testament to the stability and consistency of the material and customized application equipment.
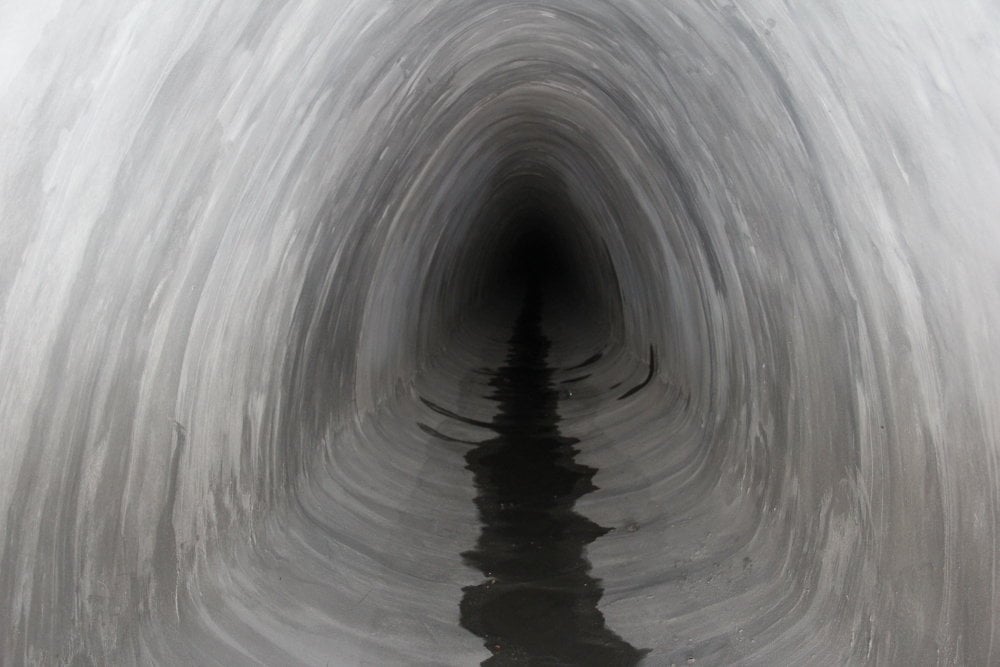
Project Challenges
In addition to standard preparation, which included pressure washing and patching of cracks and defects, 15 crumbling concrete baffles had to be removed. They were originally built into the manhole walls and each designed to cover about 60 percent of the manholes diameter to dissipate the sewer flow energy. The task of removing the baffles was not a simple one. The general contractor, Marra Services Inc., expertly patched the very large voids created when removing the baffles, ultimately bringing the manhole back to a round profile. Additionally, the sump area of the drop manhole was rehabilitated with a ½-in. stainless steel armor plate with studs embedded into reinforced high strength concrete to dissipate the drop energy and reinforce the manhole base.
The weather also presented unique challenges. Rain, snow and high winds forced a few delays in the project. On a few occasions, the wind was so strong the job was halted when it was deemed unsafe for the crane operator to raise and lower the spray application crew into the manhole. Temperature was maintained by covering the outfall with plastic sheeting and utilizing torpedo heaters. Construction staging areas and traffic maintenance also presented challenges with the location of the roadway manhole centered in the traveling lane of a T-shape intersection. Space was created by the installation of temporary concrete barriers long the lane to separate the construction crew from the traveling motorist. Traffic was maintained by installing three temporary traffic signals synchronized to permit one-way traffic movements in all directions.
Project Results
From cleaning and prep to post-installation inspection, the project took only 23 working days to complete which was performed a month ahead of the permitted schedule. By using a geopolymer, both the manhole and culvert were completely restored to full structural integrity and are designed to provide another 50-plus years of corrosion-free service. Key to this was the careful design methodology relating to proper application thickness of GeoKrete geopolymer in the critical areas of the structure.
It should also be noted that due to the depth and related hydraulic loading leading to a high amount I&I present in the manhole, Marra’s sub-contractor, Quadex Lining Systems engineering team used sophisticated engineering and design methods to ensure the success of this project. Recent, independent, third party test results taken from the project revealed that GeoKrete’s compressive strength ranged from 11,000 to 13,000 psi, which is outstanding for a field-tested sample and far exceeded the minimum of 8,000 psi required.
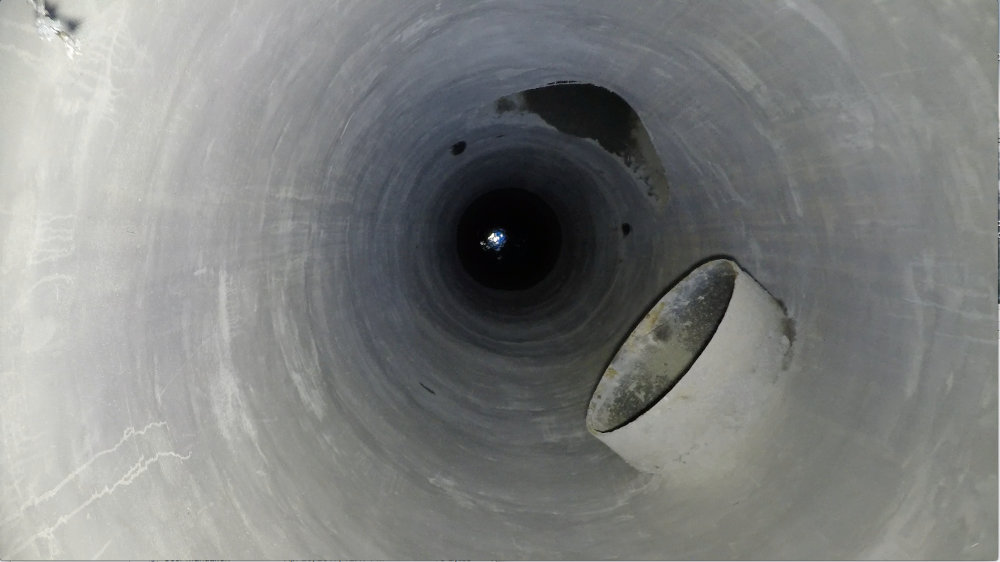
Project:
Madison-Riverside Drop Manhole Modification and Rehabilitation Project
Problem:
A 129-ft deep brick manhole constructed in 1912, along with a 350-ft brick culvert built in 1915, had reached the end of their useful lives and in a state of deterioration.
Owner:
City of Lakewood, Ohio
Designer:
AECOM
Dimensions:
– Brick Manhole: 129-ft deep and ranging from 4 ft to 8 ft in diameter
– Brick Culvert: Egg-shape 78-in. H x 66-in. W, 350 ft in length
Project Challenges:
– Shear depth of the manhole would present its own problems
– Removal of 15 large baffles built into the manhole structure
– Culvert entrance at the bottom slope with 60 degree incline making access difficult
Solution:
– Spray applied geopolymer lining system
– Job required varying thicknesses ranging from 1 to 3 in. to provide a fully structural renewal system and eliminate I&I pressure build up.
Contractor:
Marra Services, Inc.
Sub-Contractor:
Quadex Lining Systems
Source: Trenchless Technology Magazine
Henning, S. and Henning, S. (2019). Spray-Applied Lining Addresses Infrastructure Problem in Lakewood, Ohio. [online] Trenchless Technology Magazine. Available at: https://trenchlesstechnology.com/spray-applied-lining-systems-address-infrastructure-problems-lakewood/ [Accessed 20 May 2019].